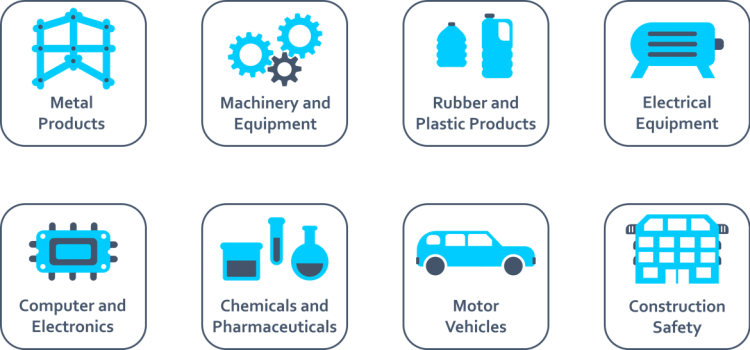
Manufacturing companies boost their competitiveness by: i) fostering the engineering process, ii) reducing the computation time, iii) solving highly complex problems, iv) improving the product quality, v) lowering the development costs, and vi) strengthening the productivity.
Use Case 1 – Optimizing Energy Consumption and Noise Emission of the Cooling Airflow for Compressors:
This use case focuses on minimizing energy consumption and noise emissions, created by the fan and the cooling airflow of compressors. This goal is achieved through introducing computational fluid dynamics (CFD) simulation within the design and development process at BOGE, in order to derive acoustics information from the flow simulation results and to influence fan selection and noise-reducing enclosure design. The resource-demanding CFD simulations have been carried out with FlowVision from Capvidia.
Technical Impact:
- reduced fan power consumption from 4 kWel to 2.75 kWel
- reduced fan noise for the fan from 82.1 dB(A) to 75 dB(A)
- reduced noise of the whole compressor by 0.9 dB(A) (15 percent reduction of noise energy)
Economic Impact:
- decreased development costs and time-to-market
- increment of market share for very silent or ultra-energy-efficient compressors
- increment in revenue by about EUR 2 million over the next 5 years
- clients could save about EUR 350.000 per year in electricity costs
Use Case 2 – Optimizing Heat Exchanger Design of Biomass Boilers through CFD Simulation:
The design of biomass boilers is currently based on the experience of the Biocurve technical staff. A prototype is designed and then the original design is improved through trial-and-error cycles. Currently, the time needed to design a prototype of a condensing biomass boiler is close to 6 months and additional 6 months are necessary to bring the prototype boiler to the market. The objective of this use case was the introduction of computational fluid dynamics (CFD) tools, specifically applied to the simulation of the heat exchanger.
Technical Impact:
- improved design of a heat exchanger, by reducing the number of pipes from 10 to 3
- decreased the weight of the boiler by 32% and the volume by 30%
- homogenized the distribution of the water mass flow throughout the water tank
Economic Impact:
- lowered development and material costs
- saved 15% of the total costs of a biomass boiler
- entered new markets with affordable prices